Fixed end bearings are radial bearings that can withstand combined (radial and axial) loads. These bearings include: deep groove ball bearing, double row or paired single row angular contact ball bearing, self-aligning ball bearing, spherical roller bearing, matched tapered roller bearing, NUP cylindrical roller bearing or NJ cylindrical roller bearing with HJ angle ring.
The following factors should be considered for the selection of motor bearing support fixed end (motor fixed end for short)
(1) The precision control requirements of the equipment to be dragged;
(2) The load nature of motor drive;
(3) Bearing or bearing combination must be able to bear certain axial force.
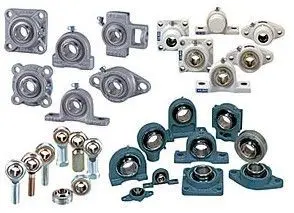
Based on the above three design elements, deep groove ball bearing is the first choice of motor fixed end bearing in small and medium-sized motor.
Deep groove ball bearing is the most commonly used rolling bearing. When using deep groove ball bearing, the structure of motor bearing support system is very simple, and the maintenance is also convenient. Deep groove ball bearing is mainly used to bear radial load, but when the bearing radial clearance is increased, it has the characteristics of angular contact ball bearing and can bear the combined load of radial and axial; When the speed is high and thrust ball bearing is not suitable, it can also be used to bear pure axial load. Compared with other types of deep groove ball bearings with the same specifications and sizes, this kind of bearing has the advantages of small friction coefficient and high limit speed, but its disadvantages are not shock resistant and not suitable for bearing heavy load.
After the deep groove ball bearing is installed on the shaft, the radial fit in both directions of the shaft or shell can be limited within the axial clearance range of the bearing. In the radial direction, the bearing and the shaft adopt interference fit, and the bearing and the end cover bearing chamber or shell adopt small interference fit. The ultimate goal of selecting this kind of fit is to ensure that the working clearance of the bearing is zero or slightly negative during the operation of the motor, so that the running performance of the bearing is better. In the axial direction, the axial fit of the positioning bearing and the related parts should be determined according to the specific situation of the floating end bearing system. The bearing inner ring is limited by the bearing position limiting step (shaft shoulder) and the bearing retaining ring on the shaft, and the bearing outer ring is controlled by the fit tolerance between the bearing and the bearing chamber, the height of the inner and outer covers of the bearing and the length of the bearing chamber.
Motor floating end bearing
The floating end of the motor is also called the free end, which is relative to the fixed end; Generally, the floating end is selected in the non driving end, but when the motor load requirements are high and the axial fit size requirements with the load equipment are not very high, the floating end will be selected in the driving end.
When the motor bearing support system is of double fulcrum and double bearing structure, when the radial load is large, the drive end is also used as the floating end. Especially for low-voltage high-power and high-voltage motors, the cylindrical roller bearing at the floating end can meet the requirements of large radial load.
The roller and raceway of cylindrical roller bearing are in line contact or repair line contact, which has large radial bearing capacity. It is more suitable for bearing heavy load and impact load. The inner or outer ring can be separated, which is convenient for installation and disassembly. This series of bearings have small friction coefficient, which is suitable for high speed and limit speed close to deep groove ball bearing. N-type and nu type cylindrical roller bearings are commonly used in motors. They can move axially between the inner and outer rings of the bearings. They can adapt to the change of the relative position between the shaft and the shell caused by thermal expansion or installation error, and can be used as free end support. However, the bearing has higher requirements for the processing of shaft or bearing chamber hole. After the bearing is installed, the relative deflection of the inner and outer ring axis should be strictly controlled to avoid the concentration of contact stress.
Compared with the fixed end bearing, in order to meet the axial displacement requirements of the rotor during the operation of the motor, the axial clearance requirements of the outer ring and the inner and outer covers of the bearing are different according to the different bearing selection.
(1) When the floating end adopts the bearing with separable inner and outer rings, for the motor with two bearing structure, the fixed end is selected as the non driving end; The outer ring of the fixed end and floating end bearings and the inner and outer covers of the bearings adopt axial no gap fit.
(2) When the floating end adopts the non separable bearing, that is, the two ends of the small and medium-sized motor are ball bearing structure. In view of the influence on the installation accuracy of the driving equipment, the driving end is the fixed end, the inner ring of the floating end bearing should be limited, and there is axial clearance between the outer ring and the inner and outer cover of the bearing; At the same time, in order to ensure the axial fit displacement requirements of the motor in operation, the radial fit between the bearing outer ring and the bearing chamber is not easy to be too tight.
The actual bearing configuration should match with the operating conditions of the motor, including the specific parameters such as clearance, heat resistance, accuracy, and the radial fit relationship between the bearing and the bearing chamber.